On Sept. 26, a Pennsylvania-based manufacturing company was cited with 21 OSHA violations following an inspection at its Millvale, N.J. facility.
While the company had a comprehensive health and safety program in place at its corporate headquarters, it failed to implement a sufficient one at the Millvale facility, which opened just last year.
Of the violations, five were willful, while 15 were serious or other-than-serious. The willful violations pertain to respiratory health, hazard communication, safety data, fall protection, and chemical hazards.
“Prioritizing production over worker safety is never acceptable and can lead to serious injuries or worse,” OSHA Area Director Paula Dixon-Roderick in Marlton, New Jersey said.
Now, the company faces $573,681 in OSHA fines.
The Violations
According to the inspection report, the metal coating company failed to:
- Provide training on respirator use and medical evaluations to determine if employees were physically capable of wearing respirators.
- Develop and implement a written hazard communication program.
- Maintain SDSs on-site, and train employees on chemical hazards.
- Provide fall protection and machine guarding.
- Train forklift operators, and certify them.
- Ensure safe use of electricity in areas where flammable paints were sprayed, and keep emergency exits unobstructed.
- Establish and follow a routine schedule for floor cleaning and removal of combustible residue.
- Ensure proper use of power tools.
Related Article: Are You Forgetting This Key Part to the Respirator Standard?
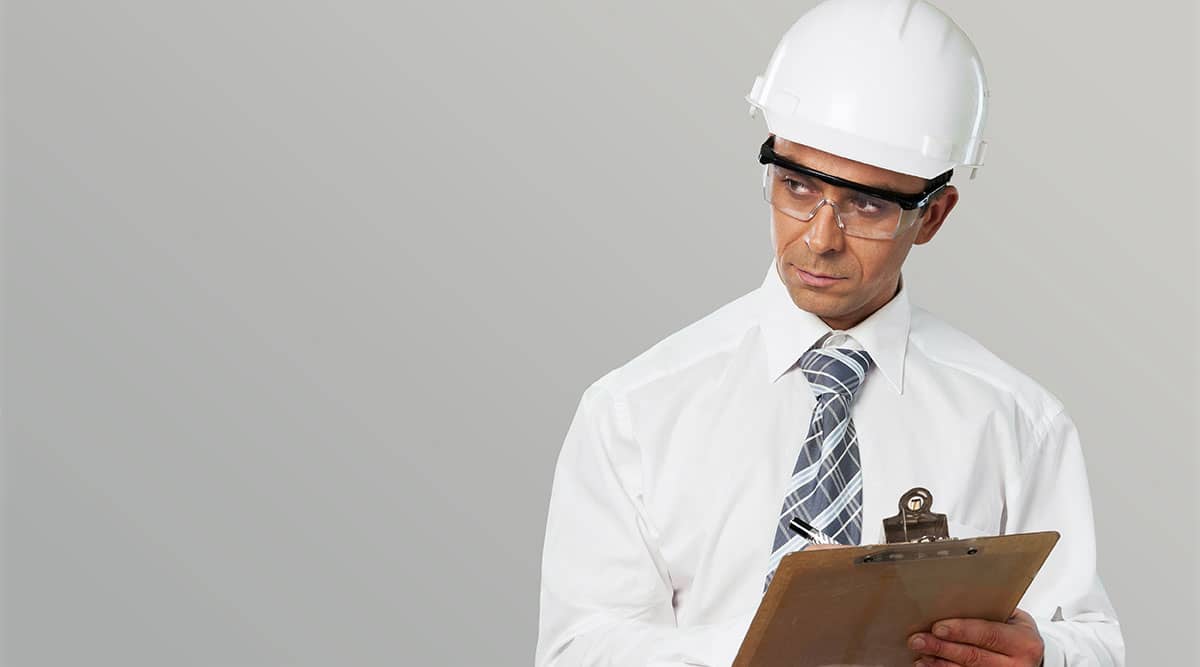
The Importance of Respirator Compliance
How important is having respirator training and medical clearance? Well, as you’ve read, OSHA believes it’s of utmost importance.
In fact, the administration requires you put a respiratory protection program in place, as per its respiratory protection standard – Standard 29 CFR 1910.134. In FY 2022, that standard landed on OSHA’s top-10 most-cited violations list with a total of 2,185 violations.
And, as citations increase, penalties also go up, as we have seen in this case. While avoiding citations is ideal, it’s not the most important factor. You also need to keep your team safe in their working environment, and ensure that they’re properly educated when it comes to respiratory health hazards in your workplace. Leaving your team untrained and unprotected not only leaves you open to fines and bad press, but it also could lead to long-term health problems for employees and coinciding lawsuits down the line.
Related Article: Top-5 Respiratory Protection Violations from 2021
For all of these reasons, you’ll need to be proactive, not reactive, when it comes to occupational health and safety.
Respirator Program Requirements
To start an OSHA-compliant respiratory program, you need to evaluate airborne workplace contaminants. Those contaminants, such as harmful dusts, fogs, fumes, mists, gases, smoke, sprays and vapors, may present a significant threat to the safety and health of workers. From crystalline silica and asbestos to toxic chemicals, you need to ensure that you know what’s in the air.
Once you’ve identified them, you’ll want to get your air monitored in order to identify and quantify airborne contaminants. That will help you to determine the level of protection your need.
Once that’s complete and you’ve determined a need for respirators, you’ll need to train your team on those hazards, and how to properly use respirators. You’ll also need to place training materials in common areas where everyone can see and read them.
Related: Download your free respirator safety training PDF here
Then, and this is critical, you must have your team medically evaluated for respirator use, which can be done online here. That’s because some employees may have underlying health issues that could keep them from safely wearing respirators during their shifts.
Once all of this is in place, you’ll need to have respirator fit tests completed before first use, if any facials features change, and once annually thereafter. There are two types of respirator fit test: Qualitative and quantitative. You can learn more about each here.
And finally, you must have a written respiratory program in place. OSHA inspectors will specifically want to see that written program during an inspection, so always have it ready and make sure you follow it.
What’s Next for the Manufacturing Company
The company has 15 business days from receipt of its citations and penalties to comply, request an informal conference with OSHA’s area director, or contest the findings before the independent Occupational Safety and Health Review Commission. Otherwise, the hefty fines will stick.
If you want to know how OSHA inspects a workplace or what to do if you’ve been cited, just click the related article link below for a breakdown.
Related article: Breaking Down the On-Site OSHA Inspection Process
To avoid facing similar consequences, you’ll need to remain prepared. How strong is your respiratory program? Is it written out and clearly understood by your team? Are you completing respirator fit tests for new hires and annually thereafter? Are your employees also medically cleared to wear respirators in the first place?
If you’re not sure, or you need some guidance, we’re here to help. At Worksite Medical, we bring the entire clinic right to your job-site, including on-site respirator fit testing, bloodwork, x-rays, and audio exams. We also offer online respirator medical clearances so your team can complete them at their convenience, from any device.
We’ll work around your schedule and make it easy to keep your team in compliance, and your workplace more productive.
To get started, just complete the form below or call us at 1-844-OCCUMED.
Let’s ensure that your company’s name stays out of the headlines next time OSHA publishes them.
***
About Worksite Medical
In most cases, OSHA requires medical surveillance testing, and at no cost to employees.
Worksite Medical makes that program easier with mobile medical testing.
We conduct on-site respirator fit tests, as well as audiometric exams, pulmonary function tests and heavy metal lab work, right on your job site. We also keep accurate, easy-to-access medical records for your convenience. You’ll keep your employees at work, and stay ahead of OSHA inspections.