As OSHA’s fiscal year ends this week on Sept. 30, the regulatory body has announced its preliminary top-10 most frequently cited workplace safety standards for 2022.
This list was presented by Patrick Kapust, acting director of OSHA’s Directorate of Enforcement Programs, at the 2022 NSC Safety Congress & Expo, which is the world’s largest annual gathering of safety professionals.
“OSHA’s annual top-10 list helps define trends so safety professionals can find the appropriate solutions,” NSC president and CEO Lorraine Martin said. “Despite advancements in workplace safety, we continue to see the same types of violations each year. It’s more important than ever employers seek education and resources to keep their workers safe.”
So, which violations made the list? Let’s break it down.
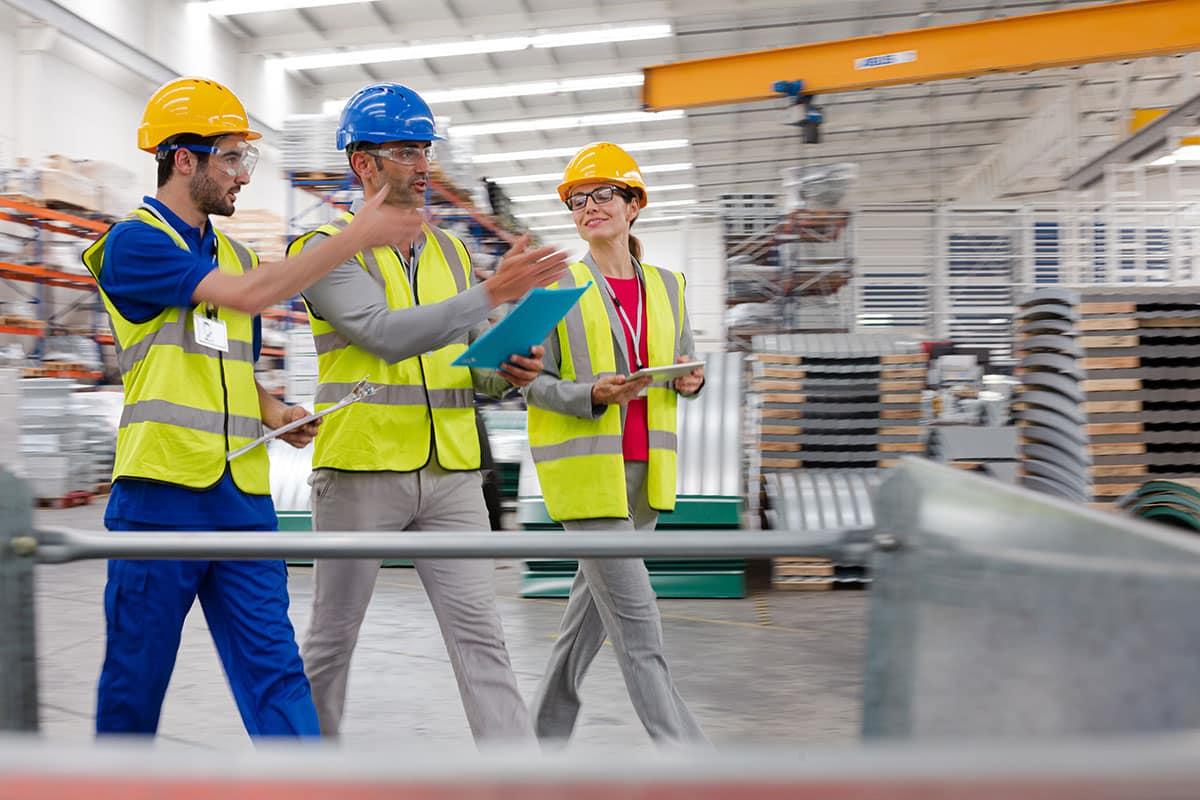
OSHA Top 10 Most Commonly Cited Violations for 2022
Some items on the list may be surprising, while others — fall protection landing in the top spot for the 12th consecutive year — aren’t so much.
Here’s the full list:
1. Fall Protection – General Requirements (1926.501): 5,260 violations
2. Hazard Communication (1910.1200): 2,424 violations
3. Respiratory Protection (1910.134): 2,185 violations
4. Ladders (1926.1053): 2,143 violations
5. Scaffolding (1926.451): 2,058 violations
6. Lockout/Tagout (1910.147): 1,977 violations
7. Powered Industrial Trucks (1910.178): 1,749 violations
8. Fall Protection – Training Requirements (1926.503): 1,556 violations
9. Personal Protective and Lifesaving Equipment – Eye and Face Protection (1926.102): 1,401 violations
10. Machine Guarding (1910.212): 1,370 violations.
A more in-depth analysis of these violations for 2022 will be published in the December edition of Safety+Health magazine, a National Safety Council publication.
Let’s take a look at Respiratory Protection in 2022
There were a few changes in this year’s list, with comparison to the 2021 top 10 violations. We saw respiratory protection drop from the second to the third position this year. The number of respiratory violations, overall, also dropped – 2,527 to 2,185.
However, that doesn’t mean it’s not still a problem. Employers are still missing on the mark on things such as the respirator medical clearance evaluation, which is a simple questionnaire that can be completed online (details here).
RELATED ARTICLE: Top five respiratory protection violations from 2021
What can you do to maintain the respiratory protection standards?
Airborne hazards are everywhere.
From silica dust to asbestos and mold, there’s plenty of risk to go around. And, if your team doesn’t feel safe within that environment, or they’re not trained to understand the toxins, it could cause lifelong lung issues. The question then becomes: Is that risk worth it?
From your perspective as an employer, you’ll also have to answer a question: Is it worth cutting corners on respiratory protection to save a few bucks now, even with the risk of OSHA fines and possible lawsuits?
In order to maintain a safe workplace, and to comply with OSHA’s respiratory standard, you’ll need to develop, maintain, and implement a respiratory protection program for your employees. Including this topic in your safety program and health and safety manual is very important if there’s any respiratory risk on any level in the line of work or industry in general.
Additionally, respirators give employees the confidence they need to stay protected and safe from dangerous vapors, dusts, smokes, mists, fogs, gasses, fumes, and sprays, and other airborne hazards. You’ll need to ensure that your team is medically able to wear them, that they’re fit tested and clean, and that you’re retesting each year, as required.
Also, make sure to download your free Worksite Medical respirator refresher guide here. You’ll want to print it and put it in a common area so that your team understands respirator safety.
As for the fit testing, medical evaluations, and even blood testing? We can help with that, and no one even has to leave the jobsite.
Schedule your on-site medical surveillance testing today, or your customized quote, by completing the form below. Let’s make sure that we keep you off of next year’s top-10 list!
***
About Worksite Medical
In most cases, OSHA requires medical surveillance testing, and at no cost to employees.
Worksite Medical makes that program easier with mobile medical testing.
We conduct on-site respirator fit tests, as well as audiometric exams, pulmonary function tests and heavy metal lab work, right on your job site. We also keep accurate, easy-to-access medical records for your convenience. You’ll keep your employees at work, and stay ahead of OSHA inspections.
What to know as an employer
In order to stay out of the SVEP, here are some things you can do as an employer:
- Increase the communication among related facilities in the corporate family about OSHA activity at any facility;
- Be proactive and correct any OSHA-cited condition at all locations after a citation at one location;
- Challenge and vigorously defend SVEP-qualifying citations because getting those citations withdrawn or re-characterized before they become a Final Order is the easiest way to get out of SVEP; and
- Challenge and vigorously defend any citations that have a high potential to be repeated.
This PDF as provides some tips and guidance.
While this is a federal mandate, all state plans must submit a notice of intent within 60 days of the initial instruction (Sept. 15) indicating whether they plan to adopt or already has in place policies and procedures that are identical to, or at least as effective as, the federal program.
***
About Worksite Medical
In most cases, OSHA requires medical surveillance testing, and at no cost to employees.
Worksite Medical makes that program easier with mobile medical testing.
We conduct on-site respirator fit tests, as well as audiometric exams, pulmonary function tests and heavy metal lab work, right on your job site. We also keep accurate, easy-to-access medical records for your convenience. You’ll keep your employees at work, and stay ahead of OSHA inspections.