The American Chemistry Council recently announced a two-year alliance with the Occupational Safety and Health Administration that will focus on improving the health and safety of workers who work in the polyurethane industry.
“We’re thrilled to be working with OSHA on making American workplaces even safer,” said Lee Salamone, senior director of the Center for the Polyurethanes Industry. “Our partnership with OSHA will build on our strong foundation of product stewardship and outreach and will help us identify additional areas of emphasis so we can better target our activities.”
Goals of the Alliance Against For Polyurethane Safety
The three primary goals of the alliance are:
- Establish a web-based training program on how to safely handle these chemicals, as well as note the risks and routes of potential exposure.
- Raise awareness of OSHA standards and initiatives regarding polyurethane and diisocyanates.
- Develop outreach efforts to educate the public on the goals of the partnership.
The American Chemistry Council is comprised of three groups: The Center for the Polyurethanes Industry (CPI), Diisocyanates (DII) and Aliphatic Diisocyanates (ADI) panels. These groups include manufacturers, distributors, and workers involved in the production of polyurethane and its materials. Most commonly manufactured as a foam or surface sealant, polyurethane is the catalyst for $74.3 billion worth of industry the United States. That said, the lucrative chemical may be having dangerous effects on about 220,000 workers nationwide.
Dangers of Polyurethane
Among the list raw materials used to make polyurethane products are isocyanates, a family of highly reactive, low molecular weight chemicals. Exposure to these substances can cause irritation of mucous membranes, which could lead to chest tightness, difficulty breathing, asthma, and/or a variety of other serious lung problems. OSHA believes that this new alliance will ensure that employers and employees will have a better understanding of the health hazards associated with polyurethane, as well as a firmer grasp on how to control exposure levels.
Currently, the American Chemistry Council is planning best practices seminars for health and safety procedures relating to polyurethane for OSHA, State Plan, and On-Site consultation staff.
Polyurethane and Medical Surveillance Testing
For employers in the polyurethane industry, medical surveillance is one of the required best practices for keeping employees healthy and well, as well as avoiding hefty OSHA fines. Worksite Medical makes the process simple by using mobile medical units on job sites across the Mid-Atlantic states.. Employers can remain OSHA compliant, and keep their workers healthy without missing a beat (or a day of work).
Avoid the risk, and let us come to you.
Schedule Your Medical Surveillance Testing Now!
Schedule Your Medical Surveillance Testing Now!
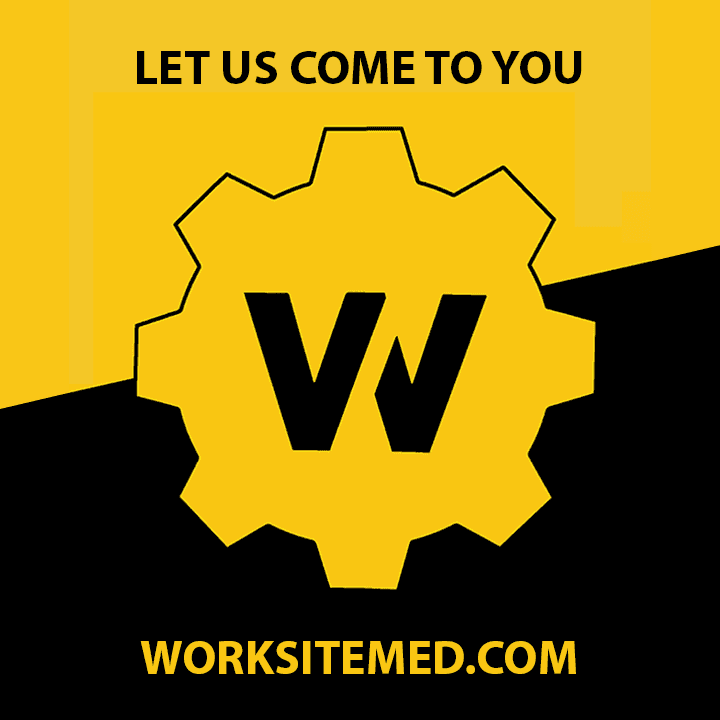