On April 3, 2023, the US Department of Labor announced the results of an investigation into a hardwood flooring mill in Ohio. Following a string of violations, the company now faces more than $333,693 in penalties and now finds itself in OSHA’s Severe Violator Enforcement Program, or SVEP.
OSHA found that the company consistently violated safety rules, resulting in three serious injuries in just five months.
This is a concerning revelation, as workplace injuries can have severe consequences for businesses, employees, and their families.
Let’s take a look at what happened, and how you can prevent such an occurrence at your worksite.
Related Article: OSHA Makes Major Update to Severe Violator Enforcement Program
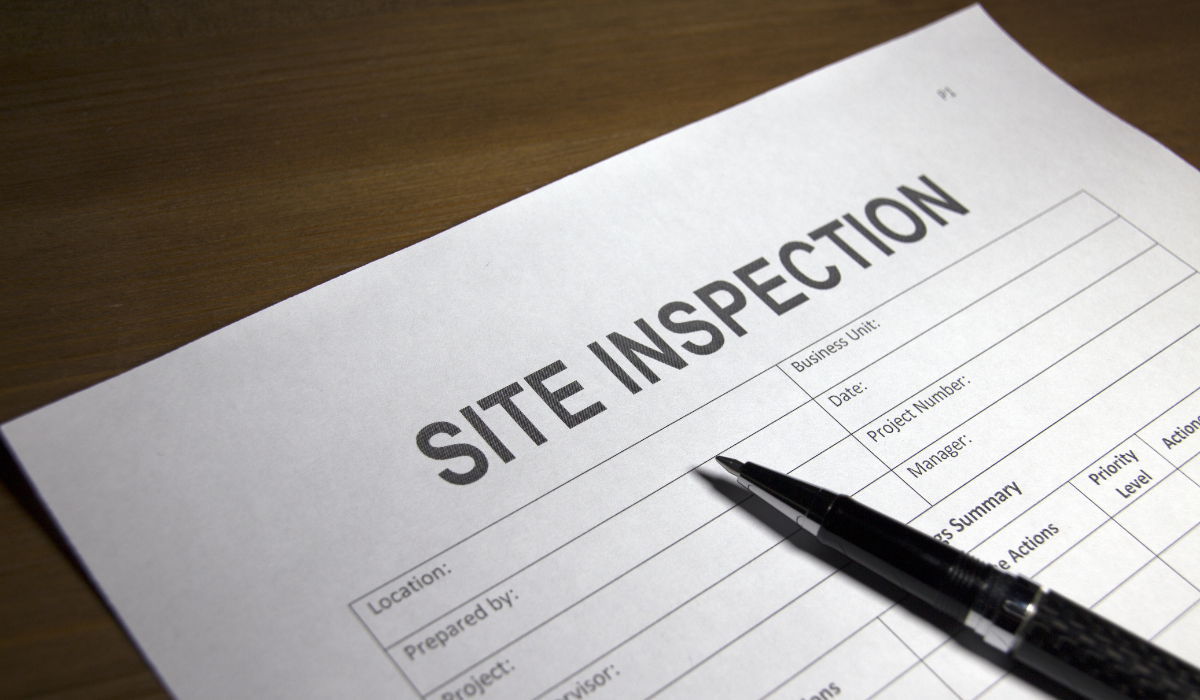
What happened?
An investigation by OSHA inspectors into the hardwood flooring mill was initiated after the third serious injury occurred in just five months. Two out of the three inspections involved workers’ injuries.
The most recent investigation occurred on October 5, 2022, after a worker’s fingertip was partially amputated after being caught in an unguarded belt and pulley.
The company informed OSHA of the injuries within 24 hours, as required.
However, during the October inspection, OSHA noted that the employees required to clean, unjam, and maintain equipment were not trained on lockout/tagout procedures, nor provided hand tools to assist with unjamming machines. Additionally, they discovered many machines lacked adequate guarding.
OSHA also noted stairs lacked guard rails, unsafe electrical practices, and workers unable to safely exit & enter their workspaces due to debris littering the floor.
The investigation also revealed that the company had consistently violated safety rules, resulting in these injuries.
Specifically, the company failed to provide proper safeguards on machinery, failed to provide personal protective equipment to workers, and failed to properly train workers on how to safely operate machinery.
Related Article: Major Retail Chain Fined $2.7 Million
Why did they end up in the Severe Violator Enforcement Program?
Ending ep on the SVEP doesn’t happen by accident (so to speak). It happens when a company consistently shows disregard for the health and safety of their team by committing willful, repeated, or failure-to-abate violations.
Companies who make it onto the list find themselves facing mandatory follow-up inspections, a blow to their business reputation, a harder time securing top employee talent, and even trouble acquiring business loans & credit.
And, considering the recent safety record of the company in question, it’s no surprise they found themselves in the SVEP.
Earlier in 2022, the agency conducted three other inspections including:
- Two inspections, opened May 24, resulting in OSHA citing five serious and one other-than-serious violations involving an unguarded chain and sprocket, lack of recordkeeping, unsafe electrical conditions and trip hazards from debris littering walking and working surfaces.
- An inspection opened July 12, 2022, after the company reported a worker who suffered a finger amputation. OSHA cited two serious violations for a lack of machine guarding.
When so many injuries occur within a short period of time, a company shouldn’t be surprised when they land in the SVEP.
Next Steps
Workplace injuries often lead to severe consequences for employees and their families.
In addition to the physical pain and suffering that employees may experience, workplace injuries can also result in lost wages, medical bills, and long-term disabilities.
Furthermore, workplace injuries can also have psychological consequences, such as anxiety, depression, and post-traumatic stress disorder.
Following the October 2022 inspection, OSHA cited the company for six repeated and 12 serious safety violations involving machine safety procedures, trip hazards for surfaces filled with debris and various electrical safety violations.
The company faces additional proposed penalties of $333,693 and has been placed in OSHA’s Severe Violator Enforcement Program.
The company has 15 business days from receipt of the citations and penalties to comply, request an informal conference with OSHA’s area director, or contest the findings before the independent Occupational Safety and Health Review Commission.
Staying out of the SVEP
Workplace safety is of paramount importance.
Not only is it the moral obligation of employers to ensure employees’ safety, it’s also a legal requirement. OSHA requires employers to provide a workplace free from recognized hazards which can lead to injuries, illness, or even death.
But, you can ensure workplace safety by implementing safety protocols and providing proper training to employees. You should also conduct regular safety audits to identify potential hazards, and take steps to address them promptly.
In order to stay out of the Severe Violator Enforcement Program, here are some things you can do as an employer:
- Increase communication among related facilities in your corporate family regarding OSHA activity at any facility;
- Use a proactive approach to safety, and correct any OSHA-cited conditions at all locations after a citation at any one location;
- Challenge and vigorously defend SVEP-qualifying citations. Getting those citations withdrawn or re-characterized before they become finalized remains a simple way to avoid the SVEP; and
- Challenge and vigorously defend any citations with a high potential to be repeated.
Bringing It Together
The recent investigation into the hardwood flooring mill reminds us all how important a strong safety culture remains.
Companies that violate safety rules can face legal consequences, including fines, penalties, and even criminal charges.
In addition to the legal consequences, companies that violate safety rules can also face reputational damage, loss of business, and decreased employee morale.
Ensure workplace safety by implementing safety protocols and providing training to employees. Issue proper PPE, and utilize regular safety audits to help identify and address any potential hazards.
By prioritizing safety, you can create a better work environment for everyone involved, reduce the risk of workplace injuries, and promote a positive workplace culture.
***
About Worksite Medical
In most cases, OSHA requires medical surveillance testing, and at no cost to employees.
Worksite Medical makes that program easier with mobile medical testing.
We conduct on-site respirator fit tests, as well as audiometric exams, pulmonary function tests and heavy metal lab work, right on your job site. We also keep accurate, easy-to-access medical records for your convenience. You’ll keep your employees at work, and stay ahead of OSHA inspections.