Ignore the rules, and you could end up paying the price. And, that’s exactly what happened to one Camden, New Jersey auto recycler and parts supplier
A comprehensive safety and health program is crucial for protecting employees and ensuring a safe work environment.
This type of program involves several key elements, including management commitment, employee involvement, safety training, and management & workforce accountability.
The U.S. Department of Labor announced on April 11, 2024, that it has reached a significant settlement agreement with a Camden Auto Recycler and Parts Supplier- one of the East Coast’s largest auto recyclers and used parts suppliers. This agreement follows litigation prompted by an investigation by the department’s Occupational Safety and Health Administration (OSHA) at the company’s Camden, New Jersey facility.
The investigation uncovered dozens of workplace safety violations, leading to affirmation of several citations and the assessment of penalties.
Let’s take a look at what went wrong.
Related Article: The Costs of Overlooking Medical Surveillance.
Related Article: Exploring 10 PPE Items for Your Hearing Conservation Program
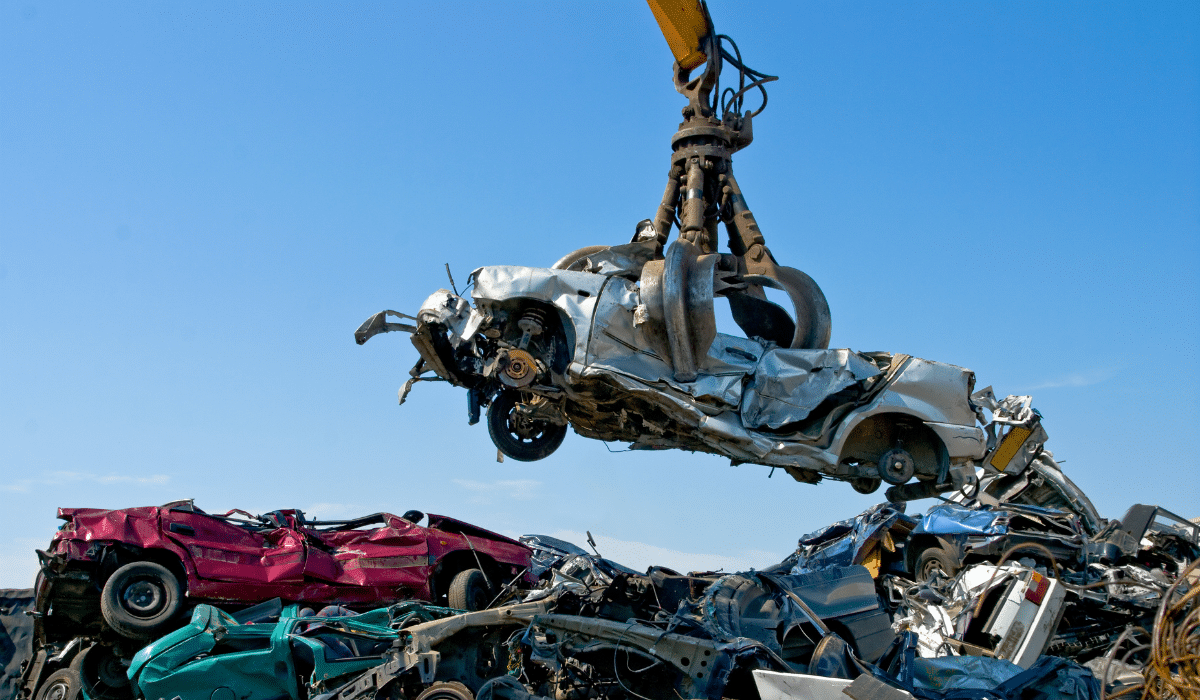
The Company’s Business Operations and Scope
The company involved purchases more than 7,000 cars and trucks each month for dismantling. Its inventory of more than 80,000 used parts is sold at its company location and its parts pickup locations in Baltimore and in Bayonne and Camden, New Jersey, and in Brooklyn, New York.
The company also sells parts online for shipment to buyers nationwide, making them one of East Coast’s largest auto recyclers and used parts suppliers.
The Settlement and Its Implications
The settlement with the company involves the affirmation of 35 citations for workplace safety violations at its Camden facility and the assessment of related penalties.
The agreement follows an OSHA investigation that identified multiple infractions, leading to two willful violations for failing to ensure employees could exit the workplace safely, and four repeat violations for not protecting workers from machine operation hazards, inadequate machine lockout/tagout procedures, and failure to control flammable liquids.
Among the 29 additional violations, OSHA identified insufficient protections from fall, electrical, and noise hazards, putting employees at risk.
The company will pay $868,628 in penalties and take action to enhance its efforts to comply with federal safety regulations, including putting a comprehensive safety and health program in place to protect its employees.
The Significance of the Settlement
The settlement between them and the Department of Labor demonstrates the importance of workplace safety and health.
By taking action to address the identified violations and implement a comprehensive safety and health program, they are making a commitment to protect its employees and ensure a safe and healthful work environment.
The Role of Worker Participation in Safety Programs
The resolution reached between the parts supplier and the Department of Labor emphasizes the importance of worker participation in safety programs.
The settlement requires enhanced programs to protect workers from serious hazards and allows them to provide input and participate in the company’s safety programs.
By involving workers in the safety process, companies can create a culture of safety that encourages employees to take an active role in protecting their own health and well-being.
The Importance of Comprehensive Safety and Health Programs
The settlement requires the company to implement a comprehensive corporate Safety and Health Management System, consistent with OSHA‘s guidance.
This system includes multiple safety audits of the facility by a third-party consultant, safety training programs based on the audit findings, and multiple avenues for workers to participate in safety efforts without fear of retaliation.
In summary, it must include the following:
- Several safety audits of the facility by a third-party consultant.
- Safety training programs based on these audit findings.
- Multiple avenues for workers to participate in safety efforts, without the fear of retaliation. And a Safety Management Committee that will review audit findings and evaluate the progress of the company’s safety programs.
Other Relevant Items of Note Include:
- Management Commitment: Ensuring that everyone in the organization, at all levels, is committed to understanding and actively participating in the safety and health program.
- Incident and Accident Investigation Policies: Implementing procedures to satisfy legal requirements and prevent future incidents, ensuring a safe work environment.
- Hazard Identification and Control: Establishing communication systems to identify and control hazards, ensuring a safe workplace for all employees.
- Ongoing Program Review: Regularly reviewing and updating the safety program to address new hazards and improve effectiveness.
- Enhanced Productivity: A safe and healthy work environment directly contributes to increased productivity, efficiency, and reduced absenteeism.
- Compliance with Legal Requirements: Ensuring adherence to regulations and standards to avoid penalties, fines, and reputational damage.
- Organizational Reputation: Organizations that prioritize health and safety are viewed as responsible and caring, attracting top talent and building trust with stakeholders
- See OSHA Publication on Recommended Practices for Safety and Health Programs.
- See OSHA INSTRUCTION on Hearing Conservation Program.
- See OSHA Publication on Voluntary Protection Programs.
- See ILO Guidelines on occupational safety and health management systems (ILO-OSH 2001).
Key Takeaways
The settlement between this company and the Department of Labor serves as a reminder of the importance of workplace safety and health.
By addressing the identified violations and implementing a comprehensive safety and health program, the company is taking significant steps to protect its employees and ensure a safe and healthful work environment. This settlement also highlights the value of worker participation in safety programs and the importance of a culture of safety in the workplace.
Implementing a comprehensive safety and health program offers long-term benefits for both employees and employers.
Employees flourish under the positive guidance of OSHA rules and regulations, gaining necessary skills to improve their overall well-being and becoming more conscious of the dangers within their workplace.
Employers also experience an increase in productivity and reduced absenteeism due to illnesses, as well as lower health care and insurance costs.
Remember: OSHA’s rules aren’t merely suggestions or requests – they’re the law.
Stay In Compliance With Worksite Medical
In most cases, OSHA requires medical surveillance testing, and at no cost to employees.
Worksite Medical makes that program easier with mobile medical testing.
Additionally, we conduct drug & alcohol screenings, on-site respirator fit tests, as well as audiometric exams, pulmonary function tests and heavy metal lab work, right on your job site. We also keep accurate, easy-to-access medical records for your convenience. You’ll keep your employees at work, and stay ahead of OSHA inspections.
With Worksite Medical, a mobile medical testing unit — we can bring all the resources of a lab to you. Our certified lab technicians can perform both qualitative and quantitative respirator tests to ensure a perfect fit.
Protect your team and your workplace now with Worksite Medical. Not sure what you need? Try our medical testing wizard here.
Give us a call at 1-844-622-8633, or complete the form below to schedule an on-site visit or to get your free quote.